Improve #4: QC vs. QI
- Manny Diaz
- Jan 30, 2020
- 2 min read
Updated: Mar 10, 2020
We have learned that the U.S. didn't value the Quality Improvement philosophy until too late. While Japan worked hard to make it happen, the U.S. kept resting in its laurels. My grandfather used to tell me that in the late 40's and early 50's Japanese craftsmanship was incredibly poor, whether it was a toy or a tool, it would break easily.
Japanese manufacturing used to rely on mass production, and quality control. No matter how hard you work, there is only so much QC that can be done for hundreds of thousands of units that only a few get checked.
Nowadays, you must have noticed that some Chinese products are the same. They even feel flimsy and break easily. This is because the quality control philosophy focuses on the finished product but not much is done in regard to process and materials to prevent poor quality. This leads us to understand what Quality Improvement is.
While Quality Control makes sure that some of the products are tested and approved, Quality Improvement examines the product, the process, the materials, the workmanship, the design, and so on. Quality Improvement focuses on examining everything from the ground up and providing concrete solutions.
We can use an apple tree as an example. This apple tree produces 1000 apples per season, however, only 500 apples are boxed and sold the rest are thrown away. Quality Control will examine each apple and select only the 50% but the rest of the apples is a total waste.
What does Quality Improvement do? Quality improvement will measure how many apples are being thrown away. Then, it will find out the root causes why this is happening. After this, Quality Improvement will measure and will also determine the solutions that address the root causes. Lastly, it will implement the proposed solutions, it will check, and will try again.
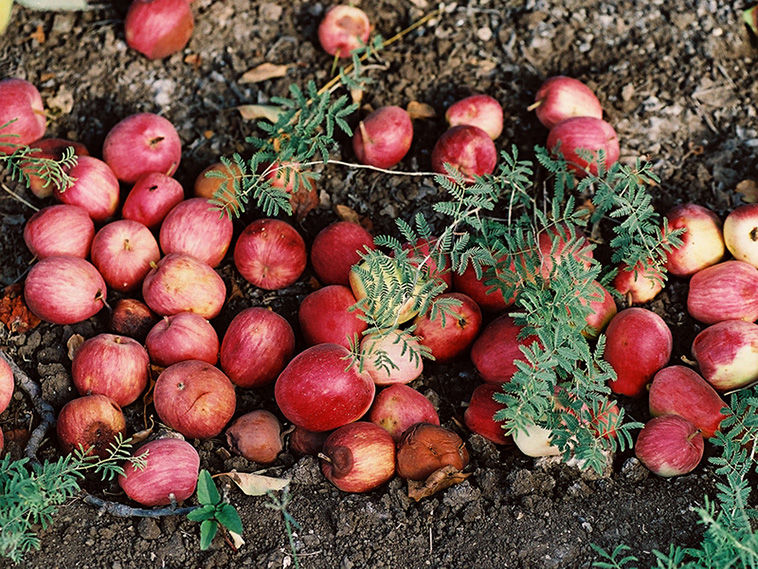
In a few words, Quality Improvement will determine that out of the remaining 500 apples that were thrown away, 300 apples were never picked up from the ground, 150 were eaten by birds, and 50 were damaged by a pest. Quality Improvement will address the problems by making sure that there is someone cutting the ripe fruit at the right time, a measure is taken to prevent birds from coming, an organic pesticide will be utilized, etc. It will try the new methods the next season, and will do this over and over until they reach 100%. This means high profits!
As we see, Quality Improvement goes to the bottom of any process to eliminate poor quality from the root, not just an examination of the fruit or the branches. It goes all the way to examining, measuring and determining and implementing solutions.
Famous companies went down because they focus on what the eyes see, not what lies underneath.
The Bible says something interesting about trees and fruit: "So, every healthy tree bears good fruit, but the diseased tree bears bad fruit. A healthy tree cannot bear bad fruit, nor can a diseased tree bear good fruit." Matthew 7:17-18
We cannot forget that true solutions to problems only come from examining everything from the root. Quality will not change unless everything is examined honestly.
Have you ever hear about the word kaizen? it originated in Japan and translates to mean change (kai) for the good (zen).
Kaizen is a philosophical belief that everything can be improved, The Kaizen philosophy lies behind many Japanese management concepts such as Total Quality control, won’t change your life overnight, but it can set significant change into motion—bit by bit.
Thank you Manny.
I find that all the previous topics (work ethics, moving forward, time management), tie in with the current one: improvement. It seems everything is connected somehow and by starting with a small change in our day we can start improvement in a general way. I've always been a fan of short-term goals set weekly or perhaps monthly. By just stating you want to, let's say, work out three days a week, or accomplish a task given at work and keep yourself accountable to it we can reach realistic goals every day. Loved the topic, there's always room for improvement.